Opto 22 Groov Epic PAC System Introduction Overview | SCADA Node Red MQTT
Introduction
In a previous tutorial on Ignition Edge, we utilized a Raspberry Pi as the hardware for the platform. As we built an application for one of our clients, the decision was to find a hardware solution that was adequate for a manufacturing environment. The Raspberry Pi is an excellent device but is not built to the same standards as to avoid potential breakdowns under higher temperatures, moisture, constant reboots, etc. We decided to investigate the Groov Epic Programmable Automation Controller (PAC) or the EPIC - Edge Programmable Industrial Controller.
The Groov Epic by Opto 22 is hardware that combines the capabilities of a traditional PLC, modern features as well as state of the art software packages. In this introductory tutorial, we will take a first look at this controller, go over the hardware features, discuss the startup procedure and finally make a few comments about the software packages that are pre-installed on the controller.
Opto 22 Groov Epic - Out of Box Experience
The Groov Epic can be purchased in many configurations depending on the needs of the end-user. However, a popular way to explore the platform is through the "Test Kit" available from a local distributor. The kit comes with the processor unit, power supply, four IO modules, and a few external devices (buttons, RTD and LED2).
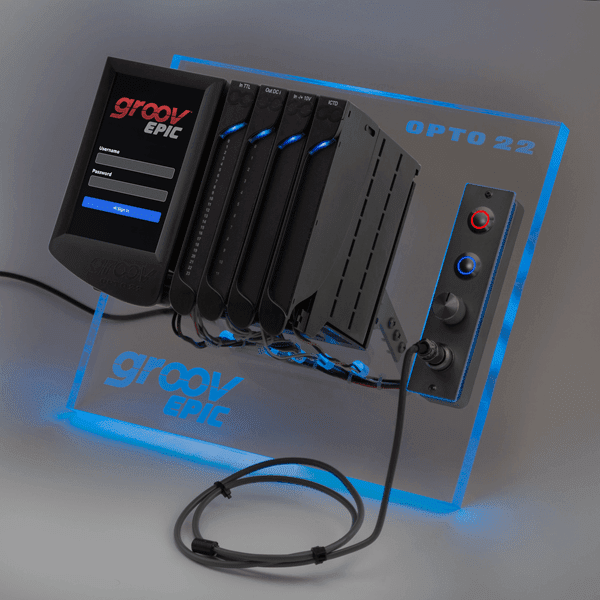
The first item of the Opto 22 Groov Epic showcased above that stands out is the LCD. The PAC features a full-color 5-inch screen through which the controller, as well as the rest of the IO, can be controlled. Next to the LCD, four input and output modules are displayed. The "Test Kit" arrives with four different modules: digital input, digital output, RTD input (analog), and analog input.
Out of the box, each module is connected to a different device to showcase the essential capability of the Opto 22 processor. The first module is tied to two buttons on the side of the controller. The second one is capable of actuating an LED for the backlight as well as a buzzer to emit sound. The third module is tied to the RTD module that will measure the temperature and send it to the first channel on the card. Lastly, the fourth module is tied to a potentiometer to demonstrate the voltage readings captured by the controller.
Opto 22 Groov Epic Hardware Specifications and Impressions
The wiring of an IO module for the Groov Epic is similar to what you'd expect from many other PLC systems. However, there are small details that one may not immediately notice. The first one being that the cover on the IO card is adjustable, thus making it easy to insert more or less cable into the controller. Certainly, a touch appreciated by field electricians working with the system. The second item is the touch capability. Each card can be touched at the top to bring up the appropriate menu that allows configuration, troubleshooting, and more. It's very convenient to be able to access this panel directly on the controller.
Groov Epic Modularity
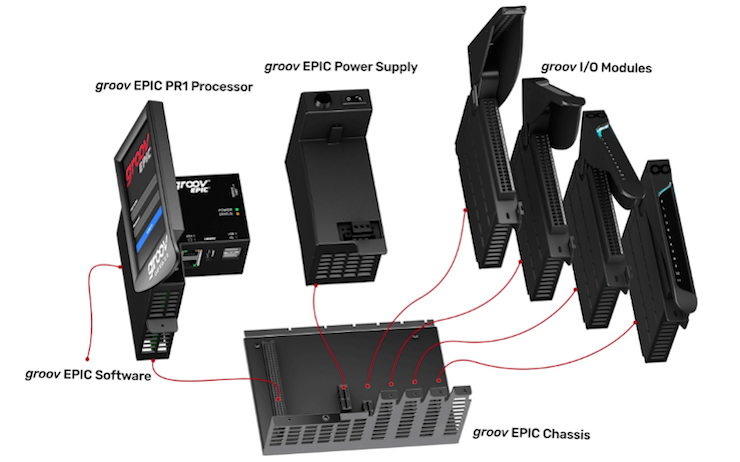
The system is entirely modular. Although the "Test Kit" comes with a four-slot chassis, it's possible to purchase a frame of 0, 4, 8, and 16 slot capacity. As one may expect, it's also possible to configure the type of input and output modules one would need for their specific application.
A wide array of input and output modules is available through Opto 22: digital, analog, private channel, high-voltage, relay, temperature probe, voltage, current, RS485, RS232, and more.
Processor Hardware Capabilities and Features
The processor of the Groov Epic has many features that some of the most expensive processors in the industry lack. It has Wi-Fi, dual Ethernet ports, HDMI outputs, and USB ports. This may not seem like a big deal. Still, the user can easily segment private to public networks for security purposes, flow the data through the PAC, display an HMI status screen directly through a non-smart TV, and navigate the menu of the PAC with a keyboard and mouse out of the box. These features would be very welcome on many other platforms.
Opto 22 Groov Epic Boot-Up Sequence
Out of Box, the processor requires the user to go through a short boot sequence, register the processor with Opto 22, set a username, set an IP for network connectivity, and load the latest firmware (optional). We decided to go through the process immediately and took about 10 minutes to get the processor in a ready state.
The firmware can be downloaded directly from Opto 22 once the registration of the processor is completed. By upgrading the firmware, the user will erase all the projects from the processor, thus making it essential to create a backup before performing this action if the processor contains project files. Note that the firmware flash may only be completed via a terminal (not the local LCD screen) and requires an Ethernet connection; enter the IP we've set in the previous step in a browser connected to the PAC controller.
At this point, once the user is logged in, it's possible to configure and interact with the PLCs software.
Opto 22 Groov Software Packages
The Groov Epic isn't just a hardware platform. It's also an ecosystem that provides the user access to some of the cutting edge software solutions within the manufacturing control systems industry. These software packages include Opto 22's solutions for PLC and HMI development, Inductive Automation's Ignition and Ignition Edge, Node-Red, MQTT protocols, Codesys, and much more. It's important to point out that the Opto 22 systems live at both sides of the (IT / OT) debate - control systems, SCADA, and Manufacturing Execution systems (MES).
There is a lot to be said about the software solutions mentioned above. We will be doing a complete coverage of each one in the following tutorials.
Conclusion
The Groov Epic from Opto 22 is an excellent industrial edge solution that comes with many features, allows for easy integration, and will have a positive impact on many end-users and other OEMs. We've explored the basics of the controller, went over the hardware, and briefly discussed the out-of-box setup process of the PAC. In the next tutorials, we'll take a deeper dive into the platform, talk about the solutions it has to offer, and bring you up to date on some of the cutting edge protocols running on the Groov Epic.