PLC Programming Comparison Instructions – NEQ | Not Equal
Introduction
The NEQ, also known as the Not Equal, instruction is used to compare two values just like the EQU Instruction. However, the key difference is that the NEQ will return TRUE if the values are not equal to each other. In other words, the outcome of this instruction is the absolute opposite of what the EQU will give us.
Just like the EQU, this instruction is critical in the control systems world. It provides an easy way to check whether a certain value is holding the value we expect and act based on the outcome.
The NEQ may operate on the exact same operands as the EQU. In fact; the only difference between the two is that their output state is inverted; just as stated above.
Example & Usage of NEQ
Here’s a real-world scenario of an NEQ instruction:
- A Micrologix 1100 Allen Bradley PLC is used to control a process.
- An NEQ instruction is used to compare an Integer N7:1 to a constant.
- The Integer N7:1 is currently set to “6” and the constant is set to “6”.
- This NEQ instruction evaluates to FALSE since the two values are equal.
- An NEQ instruction is used to compare an Integer N7:2 to the Integer N7:3.
- The Integer N7:2 is currently set to “345” while the Integer N7:3 is set to “38”.
- This NEQ instruction evaluates to TRUE since both of these integers are NOT equal.
- An NEQ instruction is used to compare a Counter “Accum” Value C5:0.ACC to the Integer N7:4.
- The Integer N7:4 is currently set to “0” while the Counter “Accum” Value C5:0.ACC is set to “56”.
- This NEQ instruction evaluates to TRUE.
Programming example in RSLogix 500:
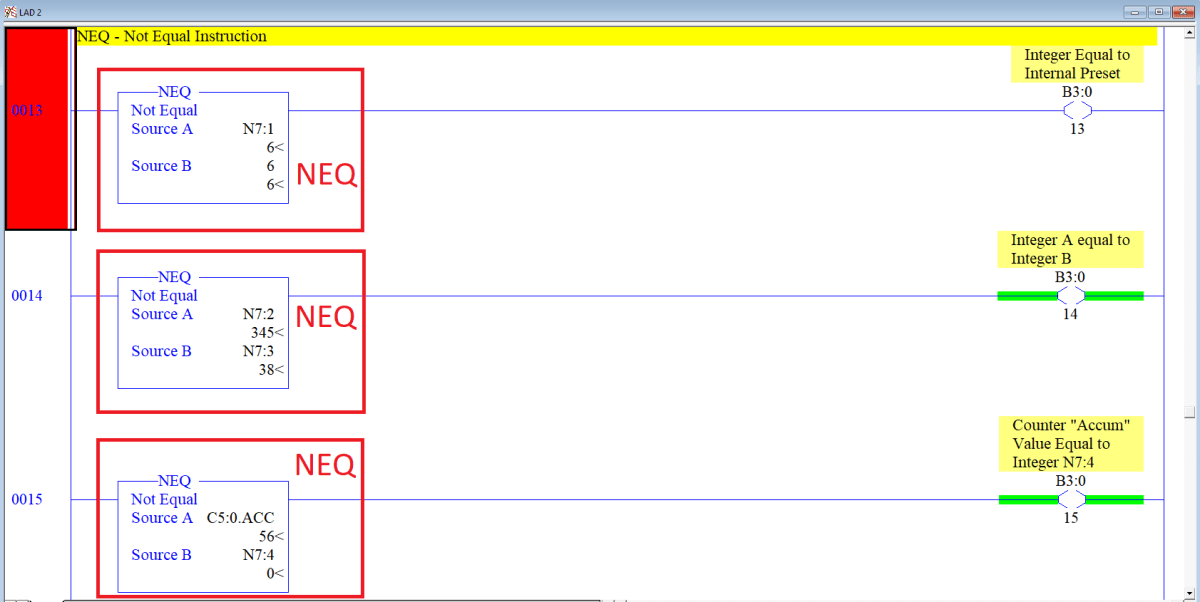
Outcome:
We’re using three different NEQ instructions to demonstrate the capabilities of the instruction. The first instruction will evaluate to FALSE because the two values stored within the “Source A” and “Source B” elements are equal to each other. One is “6” and the other is “6”. The second NEQ instruction will evaluate to TRUE due to the fact that N7:2 and N7:3 values are not the same; one is set to “345” while the other to “38”. The last instruction will also evaluate to TRUE. It demonstrates the fact that you can use the value of a Timer Construct to compare it to a value of a similar type. In this case, both are integers. Since they are “56” and “0” respectively, the NEQ evaluates to TRUE in this case.
Data Types Allowed for NEQ
The NEQ can be used to compare two values of identical types. These value can be INTs, DINTs, or FLOATs.
- Integer – You may specify each operand to be of “Integer” type.
- Float – You may specify each operand to be of “Float” or “Real” type.
Important Notes
- Note 1 – Both operands need to be exactly the same while the rung containing the NEQ instruction is being scanned. Otherwise, the instruction will evaluate to TRUE. In an instance where the value is changed in other locations for only a brief duration, the NEQ comparison may result in unforeseen outcomes.
- Note 2 – When working with constants, RSLogix 500 will not allow the user to use the constant in the “Operand A” field. The constant must be specified within “Operand B”. This limitation is not present in all software packages.
- Note 3 – The user may not specify a comparison of two constants within RSLogix 500. In other words, you may not use the NEQ instruction with “Operand A” set to 7 and “Operand B” set to 20. This case will always evaluate to FALSE which should not be used.