Tutorials /
PLC Programming Fundamentals – XIO Instruction
Beginner
PLC Programming Fundamentals – XIO Instruction
Introduction
The XIO, also known as Examine If Open, instruction perform the function opposite to the XIC (Examine if Closed). It’s a fundamental instruction for working with Programmable Logic Controllers (PLCs). This instruction can be found on the left side of a ladder logic rung and will evaluate to true if the specified bit is set to a LOW state. If that’s the case, the instruction will allow the rest of the rung to execute.
Example & Usage of XIO
Here’s a real-world scenario of an XIO instruction:
- A Micrologix 1100 Allen Bradley PLC is used to control a process.
- A normally open push button (“System Stop”) is connected to Input 1 (I0/1 of the PLC).
- An operator presses the stop button.
- The XIO instruction is tied to I0/1.
- The XIO instruction evaluates to FALSE while the button is pressed.
- The XIO instruction evaluates to TRUE while the button is released.
Programming example in RSLogix 500:
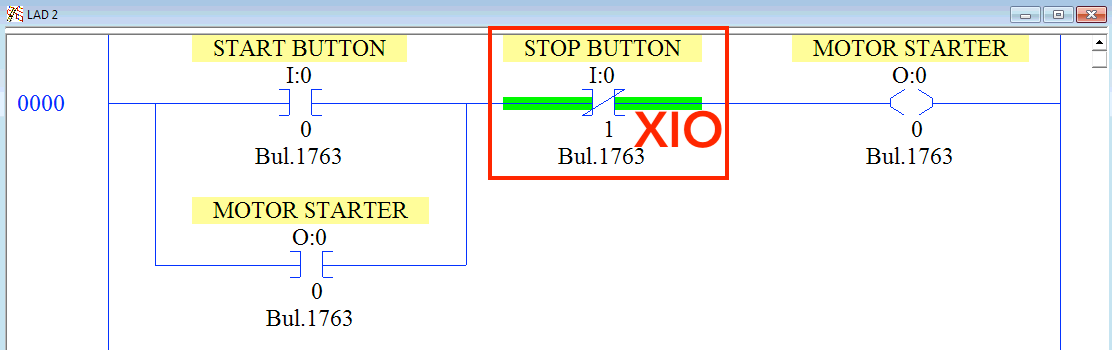
Outcome:
The XIO will stop the process when the momentary push button is pressed by the operator.
Data Types Allowed for XIO
The XIO instruction will work with the following data types within the RSLogix 500 environment:
- Boolean – The XIO may only evaluate TRUE/FALSE or 1/0 or HIGH/LOW.
Important Notes
- Note 1 – The XIO instruction was initially used to evaluate the status of inputs landed on the PLC. However, it may be used on any boolean within the program. In other words, it can examine if any boolean within the program is energized. This makes the XIO instruction powerful and versatile.